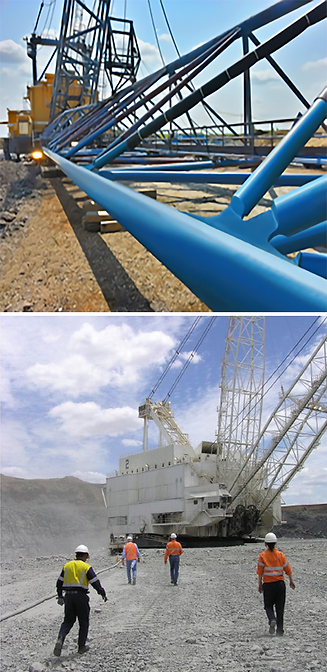
Duracluster
The smart way to upgrade tubular boom clusters and extend the life of your draglines
Save millions on dragline repairs
Eco-Friendly Design
Duracluster is our innovative design modification and repair scheme that dramatically improves the fatigue performance on draglines with tubular boom designs.
With a boom replacement costing $20 million and months of downtime, repair costs become unsustainable. Duracluster dramatically improves performance on existing tubular-boom draglines, extending life, reducing downtime and significantly lowering costs.
​
The construction of Duracluster uses a Riemann plate that provides an interface between the main chord and tubular lacings at a cluster joint. Such a design allows the lacings from the chord to be cut away, providing easy access to remove damaged or previously repaired material. The exposed chord can then be inspected and fully weld-repaired before installing the plate.
​
-
Very easy installation - only 1 week per cluster
-
Cost savings of up to 18M can be made on a major boom repair
-
Multiple clusters can be modified simultaneously
-
Significant reduction of stress concentrations, improved load paths, reduced risk
-
Dramatically extend (15-20 times) the fatigue life of tubular boom and mast structures
-
Excellent access for welding, ensures all damaged welds are repaired
-
Reduced maintenance and inspection workloads going forward
-
Easier inspection and NDT on the upgraded cluster design
24/7 Support
PROCEDURE

-
Fit plugs and plates
-
Weld, profile grind, inspect, stress relieve
-
High frequency, low amplitude ultrasonic impact
-
Relieves residual tensile stress in weld
-
Can double fatigue life
-
~400mm/min
-
Installation support provided
-
Engineered solution for boom support and bracing
-
Integral alignment jig
-
Weld procedures to relevant codes
-
Weld QA and NDT
-
Post-weld fatigue enhancement procedures
-
~ 1 week per cluster, depending on extent of chord repair required
-
Modify multiple clusters simultaneously
-
Can be done with boom suspended (requires engineered bracing)
Duracluster solves these unsustainable costs of repeat repair
Fatigue cracking at the cluster joints on dragline booms can become endemic, creating significant, unsustainable costs:
Cost of crack detection
-
Visual inspection is difficult due to the complex geometry
-
The crack must propagate through the chord wall before detection is possible
-
Substantial crack growth is required before it can be found – this substantially increases the risk of a catastrophic failure
Cost of repair
-
Cut and replace windows in lacings – this increases the potential for failure in the lacing
-
There is poor access for achieving a quality repair to the chord
-
Coping adds time and cost
-
Cranage, scaffolding adds to cost
Cost of replacement and downtime
-
A single boom replacement can cost in the region of $20 million
-
Replacement requires a three month machine outage
-
Boom replacements expose operators to a potentially high risk task with major financial consequences
